Safety protocols in handling and installing PLB HDPE ducts
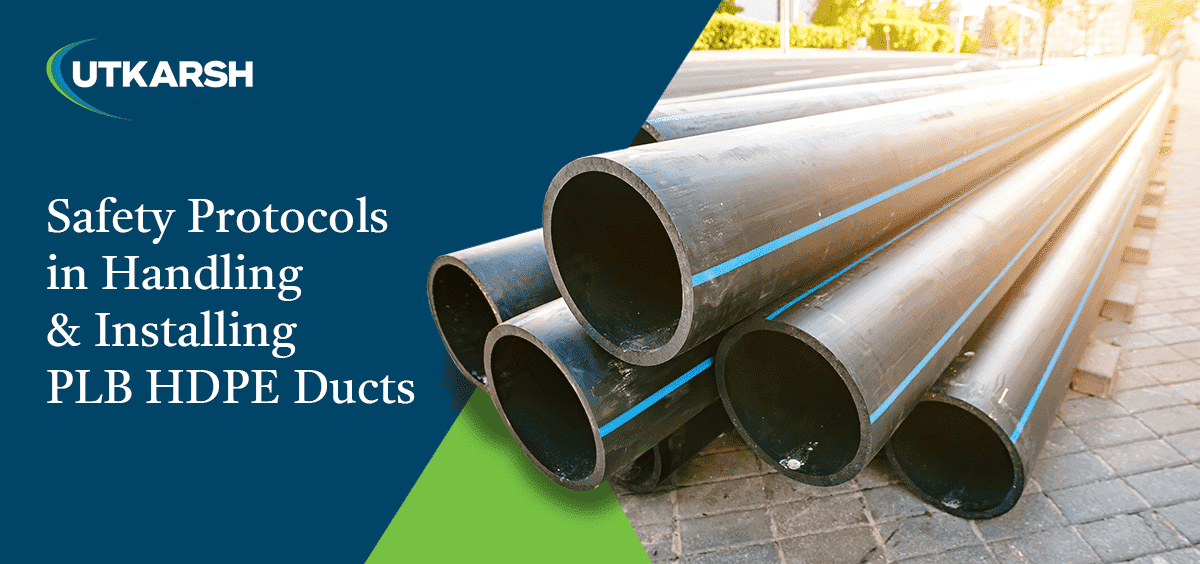
Permanently Lubricated High-Density Polyethylene ( PLB HDPE) ducts are often used to house fibre optic cables in the telecommunication sector. The increased durability of these ducts, along with their flexible applications, have made them a popular choice in the industry. However, much like any other industrial operation, working with PLB HDPE ducts can be dangerous. Workers need to take proper safety precautions to avoid accidents or injuries when working with these ducts. Here, we share some safety protocols that workers must follow.
1. Proper training and certification
Proper training and certification should be mandatory for workers who are going to work with PLB HDPE ducts. Certification and training ensure that workers are aware of important aspects, including cutting, welding, safe handling, and installation techniques.
2. Protective gear
Wearing proper protective gear when working with PLB HDPE pipes is another important aspect of safety. Safety helmets, protective eyewear, gloves and proper clothing is essential to safeguard workers during such operations. Helmets protect against falling objects and head trauma. The gloves can help keep a worker’s hands safe from sharp edges.
3. Safe cutting practices
To cut PLB HDPE ducts precisely, workers need access to equipment specifically designed for these ducts. Sharp blades ensure a clean cut, but they can also result in injuries, so workers should exercise utmost caution when cutting the ducts.
4. Fire safety
Fires can break out during PLB HDPE duct installation, potentially causing severe damage to infrastructure and harm to workers. Therefore, workers should avoid smoking near the work area, and other possible ignition sources must be kept away to prevent fire hazards. Also, fire extinguishers should be readily available.
5. Check the safety within confined spaces
PLB HDPE ducts are frequently placed in restricted areas, such as subterranean trenches. Before initiating any work, it's important to perform atmospheric tests in these confined spaces. This testing is essential to confirm the presence of adequate oxygen levels and to ensure there are no harmful gases. Also, ensuring proper ventilation is a vital safety measure that must be verified before commencing work in a confined space.
6. Handling of solvents and adhesives
When working with adhesives and solvents to join PLB HDPE ducts, workers must adhere to manufacturer safety guidelines. These chemicals can be harmful if workers are not careful, so wearing proper PPE is essential during these phases of the operation. Adequate ventilation also helps reduce the hazardous effects of these substances.
7. Trench safety
Trenches can be a dangerous place to perform industrial jobs as there is always a danger of internal collapse which can lead to serious injuries or even death. When workers need to do installation inside deep trenches, the location must have proper slopes, ventilation and protection against cave-ins.
Looking for a PLB HDPE duct and pipe manufacturer?
Explore our PLB HDPE ducts. Utkarsh's PLB HDPE ducts are manufactured from premium, UV-resistant HDPE materials and are designed for the installation of Optic Fiber and Copper Cables. These ducts are produced in line with TEC Standards and various global benchmarks. They offer enhanced protection against both natural and mechanical damages. The PLB HDPE Ducts feature a dual-layer design: an external layer of HDPE complemented by an inner layer infused with a solid permanent lubricant, which diminishes the Internal Co-efficient of Friction (ICF).
The installation of optic fibre or copper cables is made quick and straightforward, requiring fewer personnel, thanks to the design. These ducts are conveniently offered in coil form, leading to decreased installation expenses. With their design, there's minimal maintenance required. The extended lengths of the pipes mean that fewer accessories are needed. Also, these ducts are safe and free from toxins, making them user-friendly. They're optimised for the OFC Blowing installation method and are also ideal for Horizontal Directional Drilling.
Utkarsh HDPE pipes are a preferred choice for various applications due to their outstanding features and benefits. They have excellent Slow Crack Growth Resistance (SCGR) properties, ensuring durability with a lifespan ranging from 50 to 100 years. These pipes are resistant to both corrosion and abrasion, maintaining a 'C' value over 150 throughout their service life. Their chemical inertness allows them to transport acidic or alkaline fluids without degradation. Also, they can reduce surge pressures by 50-80%, ensuring leak-free joints and consequently, fewer repair incidents. These pipes also resist incrustation and scale formation, leading to lower pumping costs. Their lightweight nature makes them easy to handle and transport, eliminating the need for heavy equipment during installation. The longer delivery lengths mean fewer fittings are required, and their flexibility allows for installation over bends without necessitating additional joints.