Quality & Infrastructure
At Utkarsh Pipes & Fittings, our commitment to quality and state-of-the-art infrastructure is the cornerstone of our success as a leading pipes and fittings supplier. We take pride in our robust manufacturing processes and rigorous quality control measures that ensure each product meets the highest industry standards. Our advanced facilities are equipped with cutting-edge technology, allowing us to produce durable, leak-proof, and pressure-resistant pipes tailored for diverse applications.
Supported by a comprehensive infrastructure that includes automated polymer plants, our manufacturing capabilities boast a significant production capacity of 68,000 MT per annum. This extensive setup enables us to maintain a consistent supply of high-quality products, meeting the dynamic demands of our customers across Eastern India and beyond.
We have activated Silo systems that incorporate zero marvel technology, ensuring consistent quality throughout our manufacturing process. This innovative approach significantly reduces the need for manpower and minimises human errors, enhancing efficiency and reliability in our operations.
Quality assurance is at the heart of our operations, with every product undergoing stringent testing to ensure it is non-toxic, ultra-strong, and meets all safety and performance criteria. Our dedication to innovation and excellence is reflected in our continuous investment in advanced technology and best practices, positioning Utkarsh Pipes & Fittings as a trusted leader in the industry.
Hardik Pandya, renowned for his exceptional skills as a cricket all-rounder, proudly serves as the brand ambassador for Utkarsh Pipes and Fittings. Just as Hardik showcases his versatility on the cricket field, Utkarsh Pipes impresses with a diverse range of outstanding piping products.
Explore our Quality & Infrastructure page to discover how our advanced facilities and steadfast commitment to quality enable us to deliver exceptional pipes and fittings for every need.
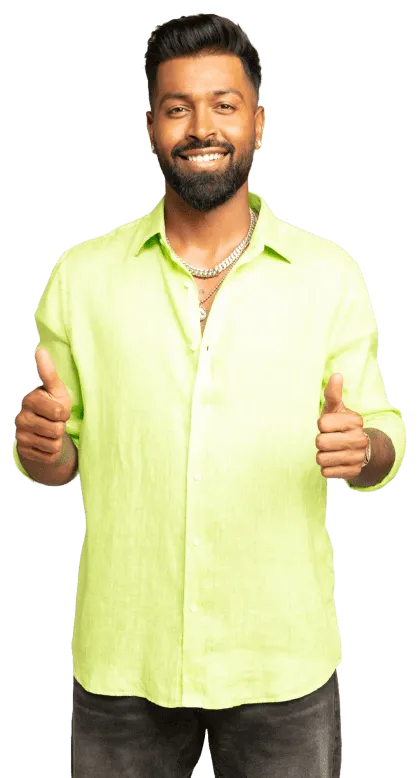
Manufacturing Process
A meticulous manufacturing process is followed for our range of uPVC pipes & fittings, right from raw material selection through final inspection and packaging.
-
Raw Materials Preparation
High-quality PVC resin and other ingredients are sourced and prepared for the manufacturing process.
-
Compounding
The PVC resin is mixed with additives through a compounding process to ensure optimal properties and performance.
-
Extrusion
The compounded material is fed into the extruder, where it is melted and formed into pipes through a die-head.
-
Pipe Formation
The extruded material is shaped into plain end PVC pipes, which are then cooled and set for further processing.
-
Internal Lab Testing
Pipes undergo initial testing in the internal lab to ensure they meet quality standards before proceeding.
-
Inspection by Third-Party Agency
A third-party inspection agency conducts thorough assessments to validate quality and compliance with industry standards.
-
Belling (if applicable)
For blue pipes, belling is performed as per IS: 12818 and ASTM D 1785 standards to ensure proper fitting.
-
Threading
Pipes are threaded as needed, with specific operations performed using CNC lathe for precision.
-
Packing & Bundling
Finished pipes are packed and bundled for storage and transport, maintaining their quality and integrity.
-
Storing of Grey Pipes
Grey pipes are stored appropriately to ensure their protection and readiness for dispatch.
-
Column Pipes Processing
Column pipes undergo threading and are subjected to further internal lab testing to maintain high standards.
-
Cutting, Grinding, and Pulverising
Any scraps generated during the process are cut, ground, and pulverised for reuse in production.
-
Final Internal Lab Testing
A final round of testing is conducted in the internal lab to confirm the quality of the finished pipes.
-
Dispatch
Once all processes and inspections are complete, pipes are dispatched to customers as per delivery orders.