Useful insights on corrosion resistance of steel tubes by one of the leading steel tube manufacturers in India
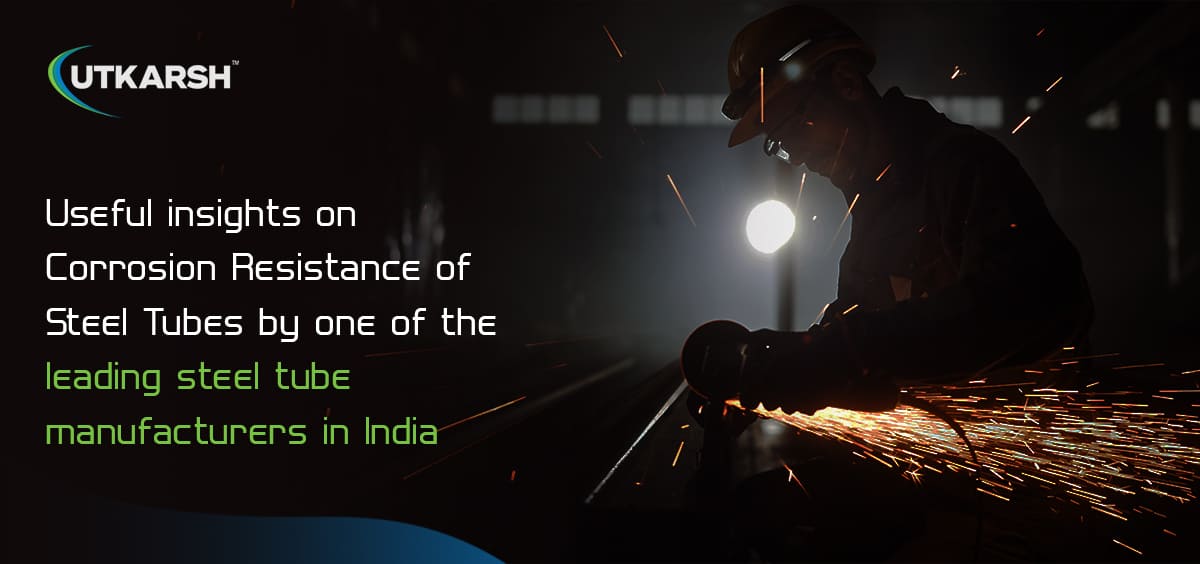
Corrosion refers to the process of atmospheric oxidation in metals,
wherein oxygen reacts with the metal to form a new layer. The most significant
type of corrosion is the rusting of iron and steel, which occurs when iron
combines with water and oxygen to produce rust. Rust appears as a reddish-brown
crust on the surface of iron. Given the extensive use of iron in various
applications, such as building construction and tools, protecting it against
rusting is crucial. Preventive measures include preventing air and water from
reaching the iron surface through techniques like painting, oiling, greasing,
or applying a protective coating of another metal. When it comes to steel,
certain alloys are known to be less susceptible to corrosion. Also, when steel
is galvanised, it becomes less susceptible to corrosion. As one of the leading
steel tube manufacturers, we share some of the useful insights on corrosion
resistance:
Factors affecting
corrosion resistance
-
Alloy
composition: The chemical composition of the steel, particularly the presence of
certain elements, greatly affects its corrosion resistance.
-
Environmental
conditions: The exposure environment significantly impacts the corrosion
behaviour of steel. Factors such as humidity, temperature, pH levels, and the
presence of corrosive agents such as chemicals, salts, or pollutants can
accelerate the corrosion process. Harsh environments, such as coastal areas
with high salt content or industrial settings with chemical exposure, require
specific corrosion-resistant measures.
-
Galvanisation: When steel
undergoes galvanisation, a protective layer of zinc is applied to its surface.
This zinc coating acts as a formidable barrier, safeguarding the underlying
steel from contact with oxygen, moisture, and other corrosive elements present
in the environment. By creating a physical barrier, the coating prevents the
corrosive substances from directly interacting with the steel, thereby
minimising the risk of rust and deterioration.
Steel is widely utilised in various applications, and tubes are among
the key uses of this versatile material. Here we will discuss the benefits of
corrosion resistance of steel tubes:
-
Durability and
longevity: Steel tubes exhibit remarkable durability, withstanding harsh
environmental conditions, moisture, chemicals, and corrosive agents without
significant degradation. This exceptional resilience translates into reduced
maintenance requirements, lower replacement costs, and minimise downtime,
making them a cost-effective long-term investment. Moreover, steel tubes retain
their strength and structural integrity over time, ensuring the reliability and
safety of diverse applications, including buildings, bridges, infrastructure,
and offshore installations.
-
Versatility: Steel tubes can
be used in corrosive industrial settings, coastal regions with saltwater
exposure, underground installations, and chemical processing plants. Their
ability to withstand corrosion extends their usability across different
sectors, including construction, oil and gas, automotive, marine, and aerospace
industries.
-
Environmental
considerations: Due to their ability to resist corrosion, steel tubes align with
sustainable and eco-friendly practices. By reducing the need for frequent
replacements and repairs, they minimise the consumption of resources, energy,
and materials associated with manufacturing new tubes. This contributes to a
more sustainable and efficient use of materials, reducing the environmental
impact.
-
Consistent
performance: Steel tubes maintain their performance characteristics over time.
They exhibit predictable behaviour, ensuring consistent flow rates, structural
stability, and functional performance in applications such as fluid
transportation, HVAC systems, and industrial processes. This reliability is
crucial in critical applications where any failure can have severe
consequences.
-
Design
flexibility: Steel tubes provide design flexibility to engineers and designers.
They can be used in complex and innovative designs, enabling the creation of
efficient and aesthetically pleasing structures. This design flexibility allows
for optimised use of space, weight reduction, and improved functionality in
various industries.
Looking for
reputed steel tube and pipe manufacturers in India?
Explore Utkarsh
Steel Tubes and Pipes. We specialise in the production and supply of a
wide range of steel pipes, including MS pipes, ERW black pipes, and GI pipes.
With a production capacity of 1,40,000 MT per annum, we are one of India's
largest processors of steel and the highest producers of galvanised products in
the country. Our manufacturing capabilities also extend to large diameter
pipes, with an approximate monthly capacity of 4000 MT.
We have advanced facilities. This includes 2 slitting lines capable of
handling lengths up to 12.5 metres, and 5 galvanising facilities that can
galvanise steel pipes up to the same length with thicknesses up to 10 mm. Our
tube mill machines operate at variable speeds between 100-120 per minute,
enabling efficient production.
Quality control is a top priority for us. We have a separate
spectrometer lab to check the chemical composition of steel grades before
commencing the production process for any kind of steel pipes or tubes. We also
have an in-house testing facility to ensure that our products meet the required
standards and specifications.
We source certain raw materials from reputed organisations, such as
SAIL and TATA. Due to our in-house logistics department, all our orders are
shipped quickly, thereby reaching customers without delays. Also, you can look
forward to pleasant and efficient after sales support.
Whether you are looking for MS tube manufacturers in India or ERW
black and GI pipes manufacturers, get in touch with us.